Quartz Ceramic Crucible
Short Description:
Quartz ceramic has excellent thermal shock resistance performance thanks to grain composition optimization. Quartz ceramic has a small coefficient of thermal expansion, good chemical stability and resistance to glass melt corrosion.
Product Detail
Product Tags
Product Details
Type | Refractory Material |
Material | SiO2 |
Working Temperature | ≤1650℃ |
Shape | Square, Pipe, etc |
Product description
Quartz ceramic has excellent thermal shock resistance performance thanks to grain composition optimization. Quartz ceramic has a small coefficient of thermal expansion, good chemical stability and resistance to glass melt corrosion.
Alumina is a kind of ceramic material that have high thermal conductivity, high abrasion resisttance, compressive strength, high temperature resistance and and thermal shock resistacne. It's also a suitalbe material for furnace use in crucible, which is low cost compared with other refractories.
There are two kinds of material for SICER Crucible, Alumina and Zirconia.
With excellent resistance to thermal shock, corrosion, and coefficient of thermal expansion, they are widely applied to the smelting process.
Alumina crucible has good acid and alkali resistance and is suitable for melting alloy and stainless steel. The maximum working temperature can reach 1600 ℃
Zirconia Crucible has excellent resistance to acid slag, and is widely used for smelting from the super alloy and the noble metal, and the optimal operating temperature is from 1980 to 2100℃.
Applications
Aluminum oxide crucible is widely used in the following application:
Used for making parts for CVD, ion implants, photolithography, and semiconductor parts.
Used for furnaces for metallurgy industry due to its ability serving under high temperature.
Used as protector for high temperature thermal couples.
Used for chemical industry with high corrosion resisttance.
Advantage
• Low thermal expansion
• Good thermal shock resistance
• Good chemical stability
• Low bulk density
• Resistance to glass melt corrosion
• Low porosity and fine surface enhance cleaness
• Superior mechanical strength and wear resisttance
• Excellent chemical resistance to acids and others
• Consistent dimensional control
Products Show
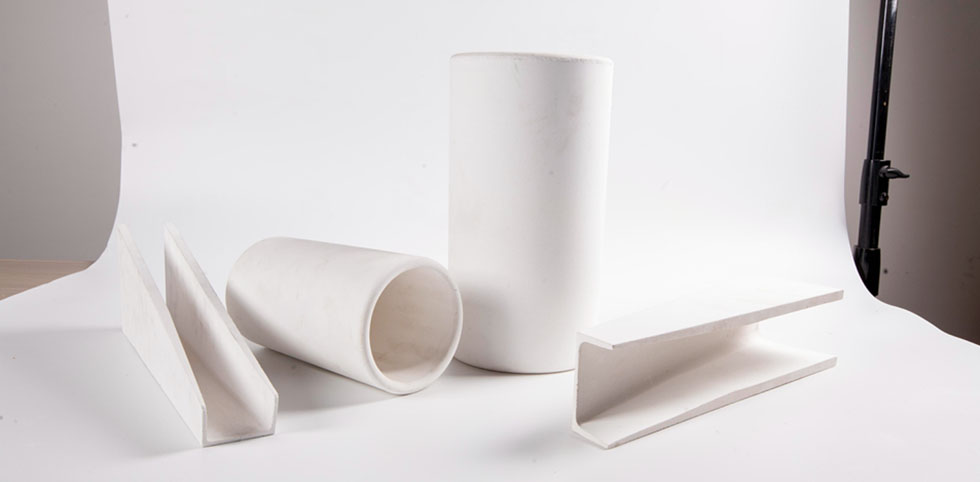